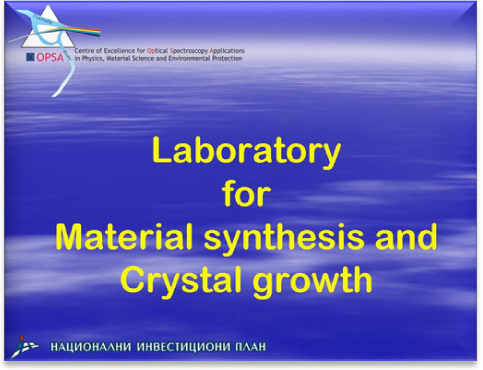
Laboratory for material
synthesis and crystal growth
consists of several crystal growth techniques such as Czochralski,
Bridgman or floating zone, thin film technology methods (thermal
evaporation, spattering, laser ablation), sol-gel technology, sintering,
etc. Here we will show only two crystal growth techniques.
Crystal growth using floating zone technique: Four
Mirror Lamp Image Furnace.
The floating zone technique is a powerful
tool for the fabrication of high quality single crystals as well as for
the purification of materials. A new four mirror optical floating zone
furnace FZ-T-1000-H-HR-I-VPO-PC (Crystal System Co.) consists of
four ellipsoidal mirrors made of Pyrex glass coated with highly
reflective aluminum. The mirrors are air-cooled in order to prevent
moisture condensation on the ellipsoidal surfaces. The principle of this
technique is that radiation from the Halogen lamps is reflected and
focused by the mirrors onto the bar sample to form a molten zone at the
tip of the feed rod. Then the molten (floating) zone is translated along
the sample length by moving the mirror stage with respect to the sample.
The crystal is grown on the solidifying end of the floating zone. In
addition, a rotation movement of the rod improves the microstructural
homogeneity during directional solidification.
In the crucibleless floating zone
technique the molten zone is kept together by capillary forces. The
optical heating is the optimal way to bring a narrow zone of the sample
to melting. In FZ-T-1000-H-HR-I-VPO-PC optical furnace the
maximum operating temperature is 2200°C
in atmosphere (air, nitrogen, oxygen, argon, etc) within the pressure
range from 5x10-5 up to 10 bars. Crystals can be obtained up
to 150 mm in length and 10 mm in diameter, with a growing rate of
0.05-27 mm/h and a 5-60 rpm rotating rate.
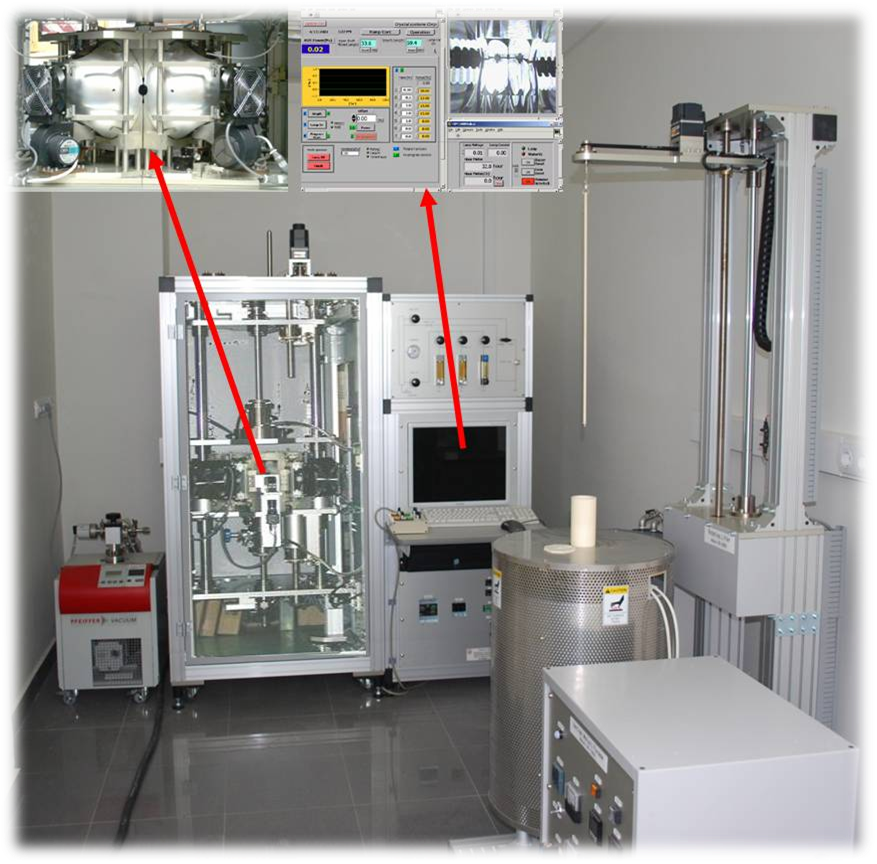
Four mirror optical furnace model FZ-T-1000-H-HR-I-VPO-PC (Crystal
System Co.)
with vertical molysili furnace model VF1800 (right).
Advantages of the four mirror floating zone furnace:
1) Stable
molten zone - Using high quality four glass mirrors and aluminum
frame, a stable molten zone can be achieved;
2) Small size -
Mirror stage moving system can diminish the scale of the furnace, so
that crystals as long as150 mm can be grown;
3) Remote
monitor and remote control system - Connect a PC to LAN system,
monitoring and controlling of the furnace can be done from anywhere in
the world;
4) PC control -
All the parameters for growing single crystals can be set and
controlled by the personal computer;
5) High
quality glass mirror - Suitable for a long-term use, and optimal
conditions are easily maintained. The surface is easy to clean, no
damage occurs;
6) Variety of halogen
lamps - The most suitable lamp can be selected from various power
lamps (150W, 300W, 500W, 1,000W and 1,500W lamp are available);
7) Monitoring by the CCD
camera - High quality color CCD camera and monitor can give real
time control of the growth;
8) Phase research by the
slow cooling float zone method - Stable molten zone by the four
mirror system can give the phase relation using the slow cooling float
zone method.
The growth of
incongruently melting or peritectic compounds
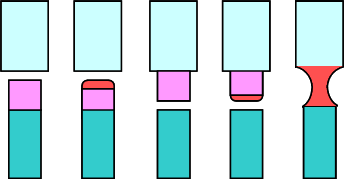 |
|
Growth of congruently melting
compounds
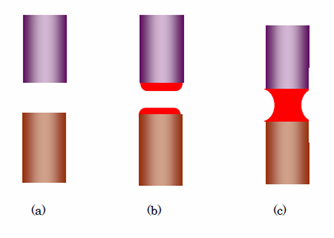 |
1) First stage: Set
the solvent zone chip on the top of the seed rod. A small amount
of starch paste can be used to fix it. The starch will be burnt
off as the temperature increases, and a small amount of smoke
will appear.
2) Second stage: Both the top of the solvent zone chip and the
end of the feed rod are partially melted, and connected without
rotation of either the upper or lower shafts. After connecting,
the lamp power is slightly decreased and the upper shaft is
retracted to separate the solvent zone.
3) Third stage: Both the end of the solvent zone chip and the
top of the seed rod are partially melted, and brought into
contact with rotation of both shafts.
4) Final stage: Adjust the lamp power to keep the molten zone
stable and to melt a few millimeters of the top portion of the
seed. After a few minutes, the crystal growth will begin. |
|
1) At the initial
stage of the heating, both the feed and seed rod are set apart
by a distance of a few mm;
2) As the heating progresses, both ends of the feed and seed rod
will begin to melt;
3) At this stage, the upper feed rod is moved to downwards until
it touches the seed rod. Finally, the length of the molten zone
is adjusted so that its diameter is almost the same as that of
the feed and seed rod |
Advantages of Floating zone in comparison
with the Czochralski method:
1) High purity crystals can be grown without contamination from the
crucible;
2) Can be applied to grow oxide, metal and other materials;
3) Can grow single crystals of incongruently melting materials;
4) Low cost of the crystals growth;
5) Can be applied in phase research by the slow cooling float zone
method.
Crystal growth by the Czochralski method
The
Czochralski process is a method of crystal growth used to obtain
single crystals of many semiconductors (e.g. silicon, germanium
and gallium arsenide), optical materials (e.g. ruby, sapphire,
YAG, Bi12GeO20), metals (e.g. palladium, platinum, silver,
gold), salts and some hand made, (or "lab") gemstones.
High-purity starting materials or polycrystals are melted down
in a crucible, which is usually made of quartz, platinum,
molybdenum, alumina etc. A seed crystal, mounted on a rod, is
dipped into the melt. The seed crystal rod is pulled upwards and
rotated at the same time. The dopant impurity atoms can be added
to the melt. By precisely controlling the temperature gradients,
the rate of pulling and speed of rotation, it is possible to
extract a large single-crystal cylindrical ingot from the melt.
This process is normally performed in an inert atmosphere, such
as argon, or in an inert chamber, such as quartz. |
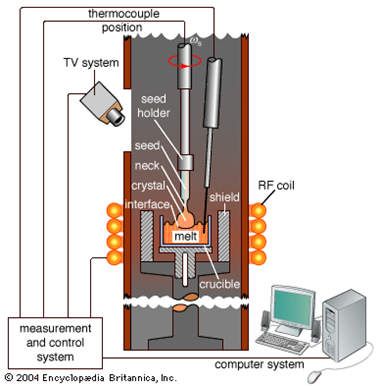
|
Occurrence of unwanted instabilities in
the melt can be avoided by investigating and visualizing the temperature
and velocity fields during the crystal growth process.
The process is named after Polish scientist Jan Czochralski, who
discovered the method in 1916, while investigating the crystallization
rates of metals.
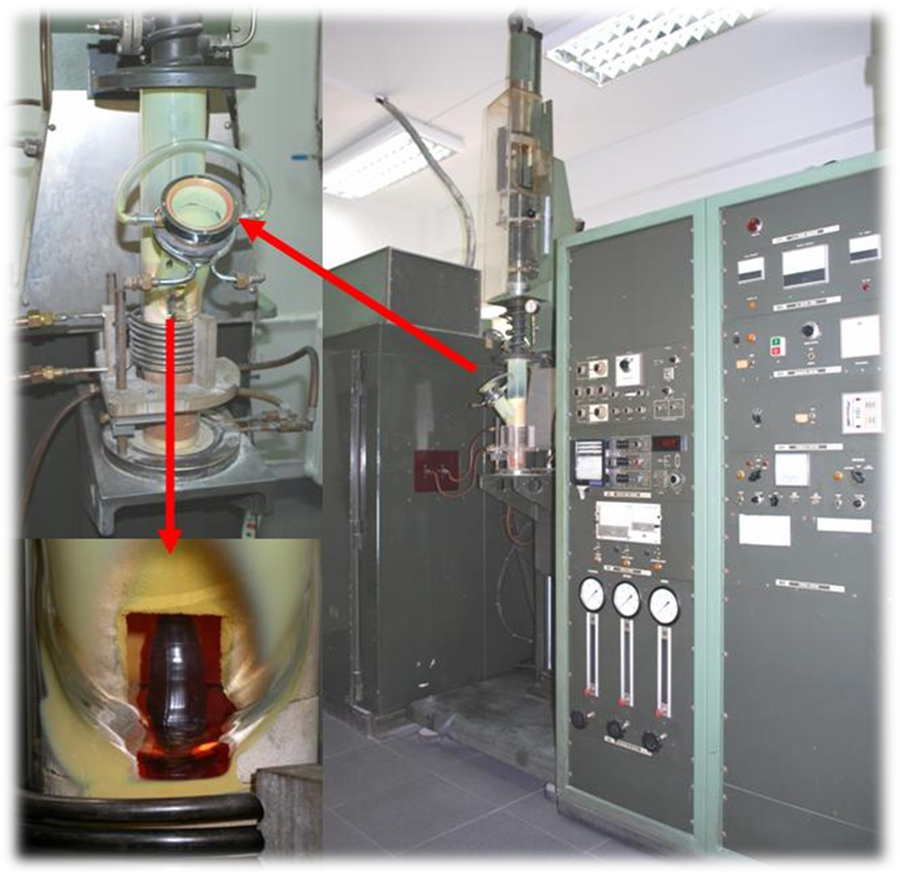
Czochralski crystal growth system (Metals Research Co). Crystal ingot is
Bi12GeO20.
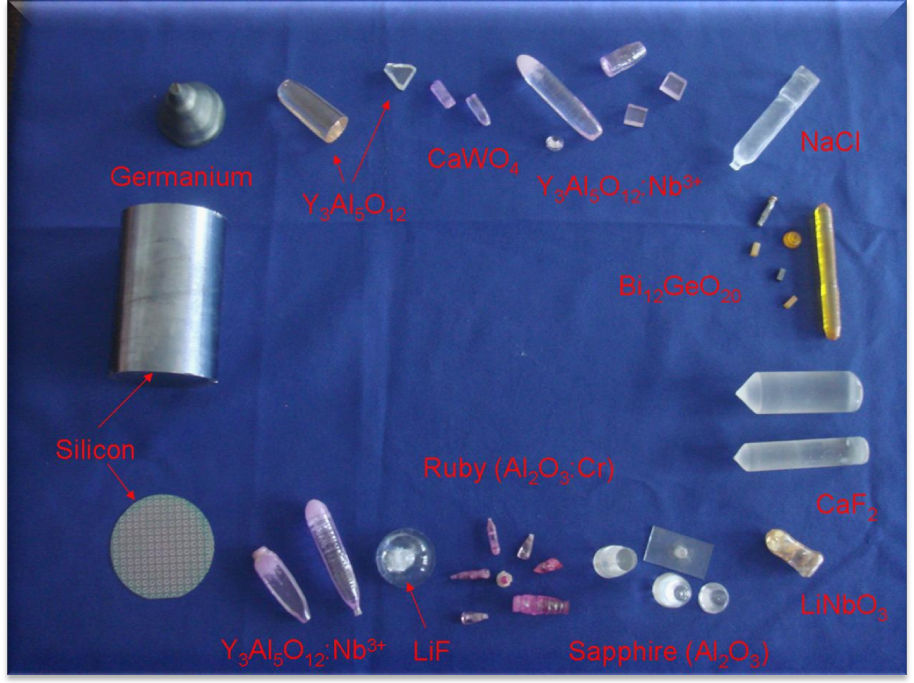
Single crystals of several semiconductors
and optical materials obtained in our laboratory using the Czochralski,
Bridgman and floating zone techniques.
|